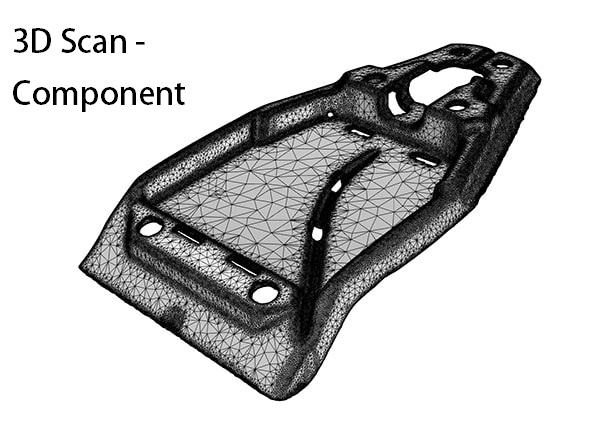
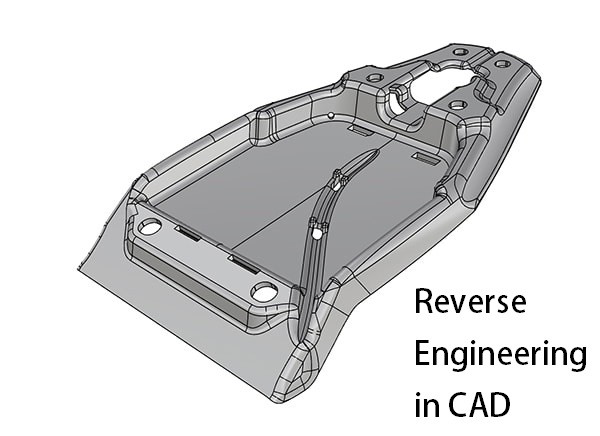
EXPLANATION OF REVERSE ENGINEERING THROUGH 3D CAD SOFTWARE - INDIVIDUAL STEPS
Manual Reverse Engineering in CAD.
Optimal CNC data are reconstructed from the component using a 3D Scan.
REVERSE ENGINEERING WITH CAD SOFTWARE
Reverse Engineering is the manual reconstruction of a point cloud in CAD
A point cloud is imported into the CAD software. Reverse engineering then replaces the points of the STL network with areas of the same size. Deviations and damage are removed from the scan.
Explanation of reverse engineering using the following example:
The imported mesh of a machine component contains an area that contains a flat and rectangular area with the dimensions 85 x 150 mm. This area is represented in the point cloud by approx. 3000 points. In the cross-section you can also see that these points are not on the same plane, but rather deviate by 0.05 mm upwards / downwards. These 3000 points were generated by the scanner. The deviation of 0.05 mm is the tolerance of modern 3D scanners. The designer now creates a rectangle with a size of 85 x 150 mm, replacing the area of 3000 points.
When all points have been replaced with new, reconstructed surfaces, this data record can be saved as a surface or volume model in STEP, or as native data, in the data format of the CAD software.
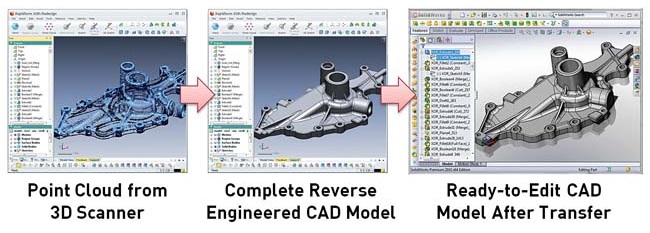
The advantages of this CAD data are as follows:
1. Reverse engineering removes scan deviations.
2. Reverse engineering reduces the amount of data considerably.
3. Reverse engineering creates surface or volume models that can be further processed in CAD.
There are other advantages such as - The removal of damage, optimization of the surfaces (automotive). We are at your disposal for a free telephone consultation without obligation. You can reach us from Monday to Friday between 9 a.m. and 6 p.m. on the phone number +49 2834 4629 681, or by email at [email protected]
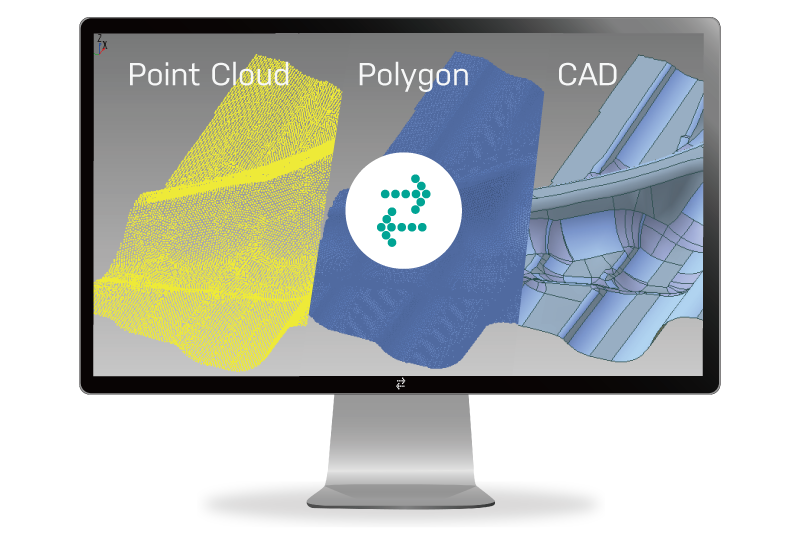
Reverse Engineering Procedure
Reverse-Engineering in Parametric Data
Create CAD Data with Parametric History
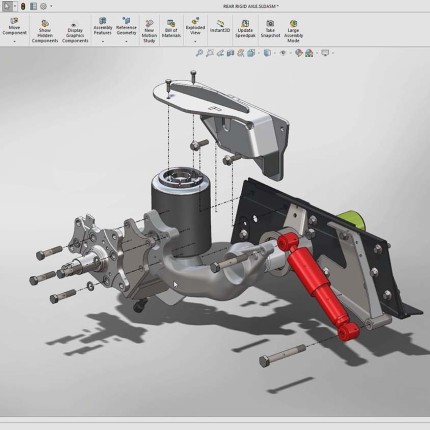
SOLIDWORKS
1. Solidworks – Reverse-Engineering in native Solidworks data with Construction history
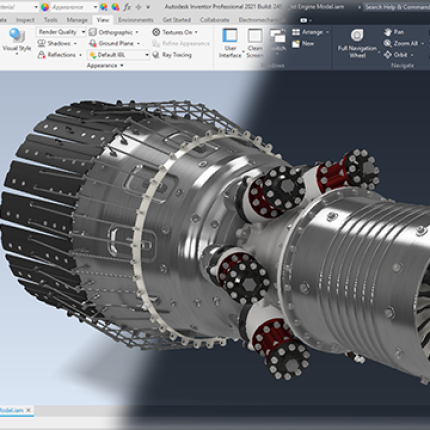
AUTODESK
2. Autodesk – Reverse-Engineering in native Autodesk data with Construction history
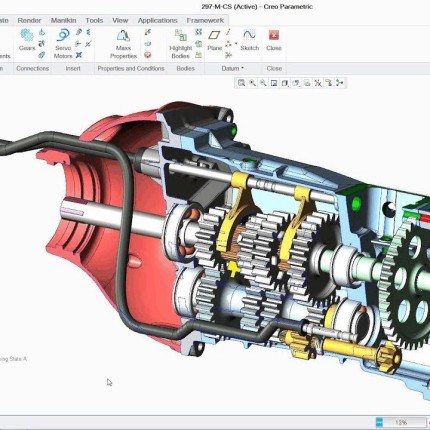
CREO
3. CREO – Reverse-Engineering in native CREO data with Construction history
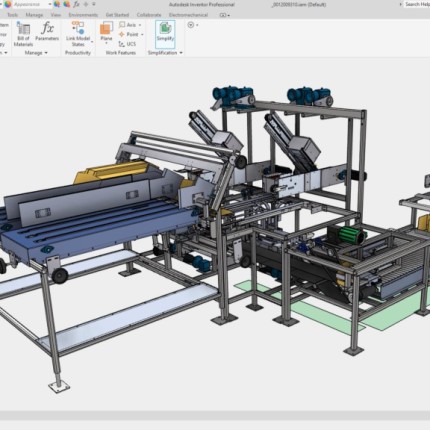
INVENTOR
4. Inventor – Reverse-Engineering in native Inventor data with Construction history
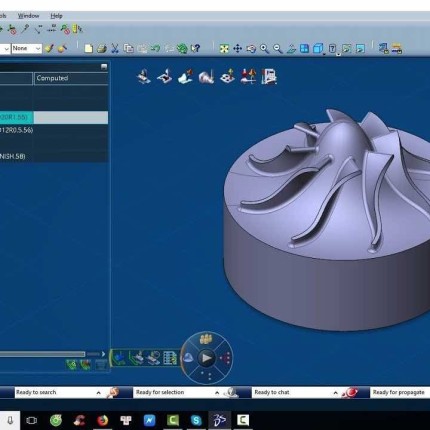
CATIA
5. CATIA V6 – Reverse-Engineering in native CATIA V6 data with Construction history
Reverse-Engineering in Volume-Data
Create CAD files out of Scan Data
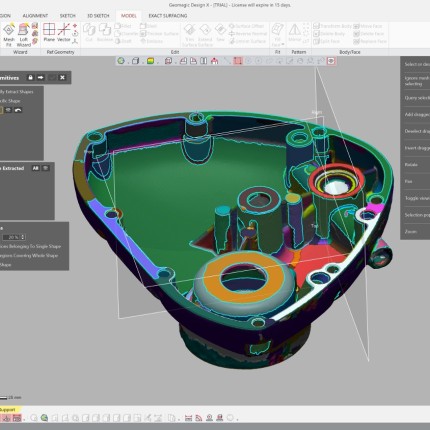
DESIGN X
1. DesignX – Reverse-Engineering in STEP
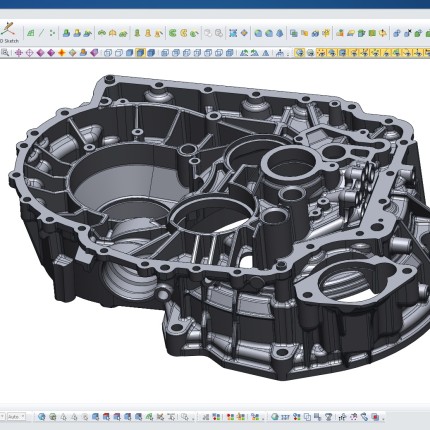
DESIGN X
2. DesignX – Reverse-Engineering in IGES
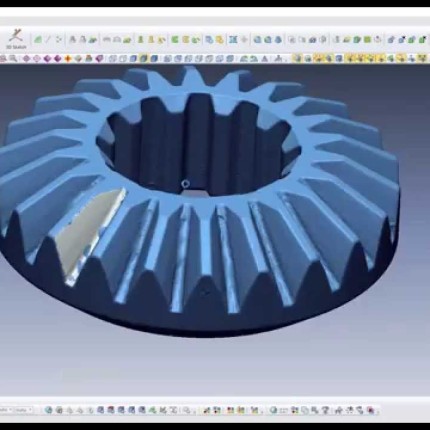
SIEMENS NX
3. SiemensNX – Reverse-Engineering in STEP
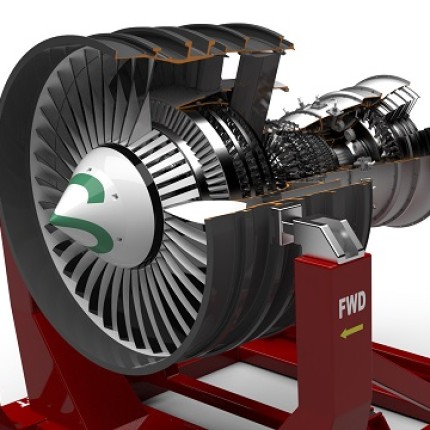
SIEMENS NX
4. SiemensNX – Reverse-Engineering in IGES
OUR SERVICE
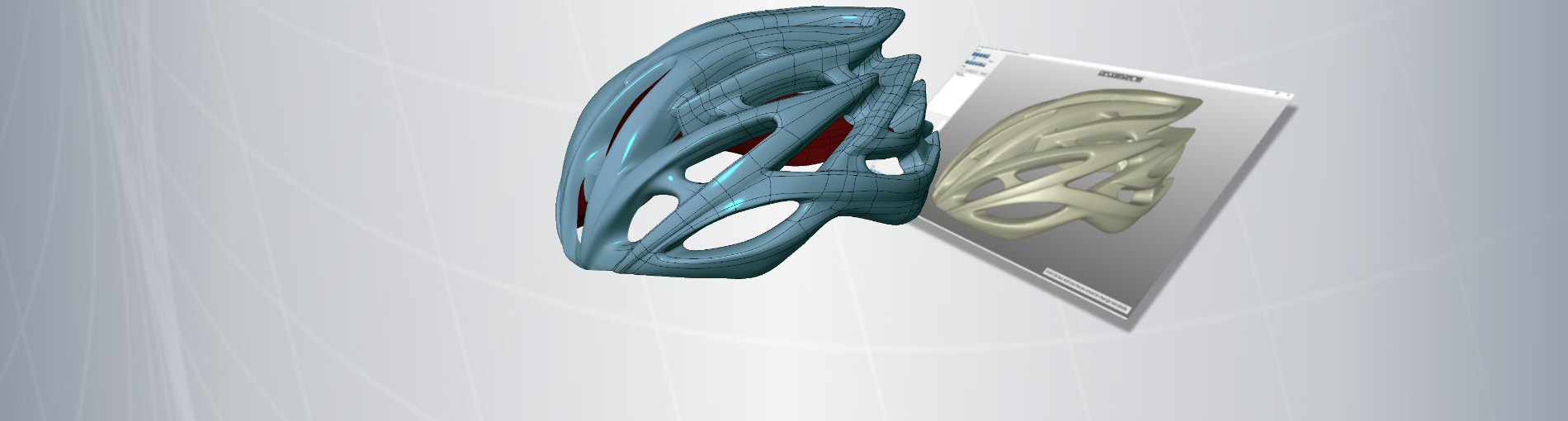
Reverse Engineering - consulting on 3D technologies
Our TEAM, of currently approx. 30 engineers, processes 3D scan data for import into your CAD software. As a service provider for reverse engineering, we have a network of partners and colleagues who offer almost every service in the 3D area. We assist in creating a 3D scan, data preparation and we can help with 3D printing. For your toolmaking processes, the scanning of a model and converting it into CAD / CAM dataset can provide a significant time and cost advantage. - We are happy to help.
Reverse Engineering - Quality and benefits through digitization
Increase your product quality by creating accurate 3D scans. Your production benefits from optimally prepared data for the tool design. The quick replacement of your component offers new possibilities in communication.
EXPLANATION OF REVERSE ENGINEERING - DO YOU HAVE A QUESTION?
If you submit your contact information here, you will get a link to download the Sample Reverse Engineered data. Take your time to evaluate the quality of our Reverse Engineering or use the 'Message' field to submit a request or question to our team of experts.
PARTNERS
Our cooperation partners...
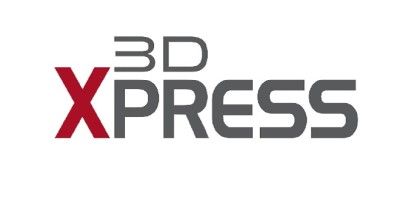
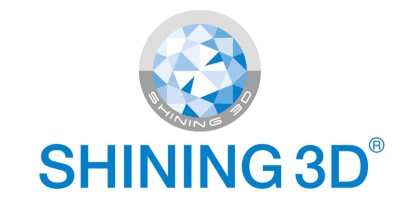